Electric vehicle (EV) cable harnesses are one of the most popular topics in the field of wire processing today. This is a very new and exciting market, which is rapidly changing with the emergence of new technologies. For those who wish to expand into this market, it is crucial to understand the process of effectively automating MV Aerial Bundled Cable connector components.
The high-voltage connectors used in EV applications have many components, so multiple process steps must be executed in a specific order. Although most customers hope to automate each process step, they often cannot justify the cost of a fully automated system.
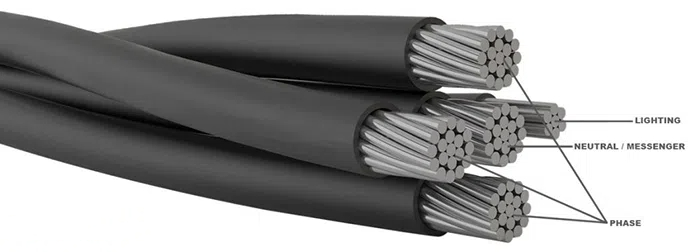
Some process steps are more challenging and require higher accuracy. For example, removing the foil layer or cutting the shielding layer is more critical, as the performance or safety of the connector may be significantly affected. In addition, almost all connector and cable types require some process steps, and only certain specific connectors require other process steps. Based on the number of specific connector families, automation may be more meaningful if only key or common steps are followed by simpler or less common steps through manual operation. However, if the quantity proves it reasonable, it can all be automated.
Currently, over 97% of high-voltage applications require shielded MV Aerial Bundled Cable, whether multi-core or coaxial. HV application range from 3mm2 to 120mm2 single core (coaxial) or 2 × 2.5mm2 to 5 × 6.0mm2 multi-core cable, used for a wide variety of single cable and multi cable connectors. Therefore, customers who are seriously considering expanding their products to HV cable components must focus on providing automation solutions that are not only high-precision but also fully flexible, in order to protect any investment knowing that future processing requirements may change. It is important that the systems can be expanded on-site so that they can adapt and evolve with your business.
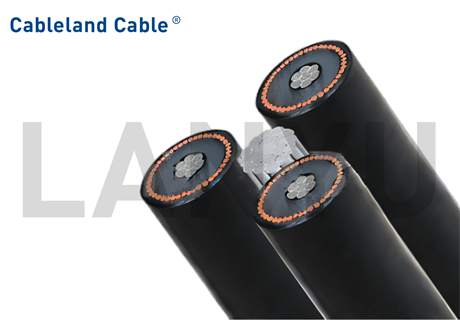
Due to their different functions and/or structures, different connectors typically have very different individual process steps. However, there are some basic steps that apply to almost all of these steps, which are related to correctly stripping the cable and loading the ferrule.
If the high-voltage cable has a foil layer during processing, it must be stripped clean and flush with the outer sheath without leaving any marks. This is almost impossible for fixed blades. Unless the foil is bonded to the outer sheath, it is certainly possible to use a laser system. The laser system requires space for the laser to reach the foil. However, if the foil is bonded to the outer sheath, any pulling of small pieces may cause uneven tearing of the foil. In addition, the laser does not cut areas where the foil overlaps.
Shielded high-voltage cables are very challenging to correctly cut the shielding layer using traditional rotary stripping devices, especially if the cable has non concentric or non circular layers. The integrity of the dielectric and filler is crucial for the normal performance of the cable, and traditional rotary stripping machines pose a risk of damaging the inner layer. The anvil and stamping system ensure that the inner layer is not damaged and the shielding layer is cut 360 ° clean and evenly around the cable.